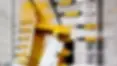
Powder Coating Automatic
Plant
Investing in an automatic powder coating plant can improve coating quality, reduce waste, and increase production efficiency.
Powder Coating
.webp)
Automatic
Powder Coating Plant
An automatic powder coating plant represents the pinnacle of efficiency and precision in surface finishing technology. This advanced facility is designed to streamline the powder coating process, from initial preparation to final curing, with minimal human intervention.
At the heart of the operation are sophisticated conveyor systems that seamlessly transport components through various stages, including cleaning, pre-treatment, powder application, and curing. Automated robots or electrostatic guns precisely apply the powder coating onto the surfaces, ensuring uniform coverage and thickness.
he plant is equipped with state-of-the-art controls and monitoring systems to regulate parameters such as temperature, airflow, and coating thickness, ensuring consistent quality and adherence to specifications.
Additionally, advanced filtration systems are employed to minimize waste and environmental impact by capturing overspray and recycling unused powder. Overall, an automatic powder coating plant represents the epitome of modern manufacturing, combining efficiency, precision, and sustainability to deliver high-quality coated products across industries.
Application:
An automatic powder coating plant applies a durable finish to surfaces with electrostatically charged powder particles, ideal for industries like automotive, appliances, and architecture.
Technology:
Powder Coating OVEN
Standard/
Customization
Customised option is available as per requirement
Delivery:
4 to 6 weeks
Features:
-
Conveyor System: An automated conveyor system is often the backbone of a powder coating plant, transporting parts or products through the coating process seamlessly.
-
Pre-treatment Stage: This stage involves cleaning and prepping the surface of the parts to be coated, often through processes like degreasing, rinsing, and applying chemical treatments to enhance adhesion.
-
Powder Application Equipment: Automated powder application equipment such as electrostatic spray guns or powder coating robots are utilized for precise and consistent coating application.
-
Recovery System: A powder recovery system is essential for reclaiming excess powder and recycling it for future use, minimizing waste and reducing operational costs.
-
Curing Oven: After the powder is applied, parts are moved through a curing oven where the coating is heated to the appropriate temperature, allowing it to melt, flow, and form a durable finish.
-
Cooling Zone: Parts may pass through a cooling zone after curing to ensure they are cooled down to a safe handling temperature before further processing or packaging.
-
Quality Control Stations: Inspection stations equipped with lighting, magnification tools, or automated inspection systems are incorporated to ensure the quality and consistency of the coated parts.
-
Data Monitoring and Control: Modern powder coating plants often feature advanced control systems that monitor process parameters such as temperature, conveyor speed, and powder flow rate, allowing for real-time adjustments to optimize efficiency and quality.
-
Environmental Controls: Environmental considerations are paramount in powder coating plants. Dust collection systems and exhaust ventilation help to control powder overspray and maintain a safe and clean working environment.
-
Automation and Integration: Many powder coating plants are designed for high levels of automation and integration with other manufacturing processes, facilitating seamless production workflows and minimizing manual intervention.
-
Flexibility and Customization: Some plants are designed to accommodate a wide range of part sizes, shapes, and materials, with adjustable conveyor speeds, spray patterns, and curing profiles to accommodate varying production requirements.
-
Safety Features: Safety features such as interlocks, emergency stops, and protective guards are integrated into the plant design to ensure the safety of operators and prevent accidents.
Material Compatibility:
-
Substrate Material: Determine if the substrate material (e.g., metal, plastic, wood) is compatible with the powder coating process.
-
Surface Condition: Ensure the surface is clean, dry, and free from contaminants like oil, rust, or scale for effective powder adhesion.
-
Heat Resistance: Verify that the substrate can withstand the curing temperatures required for powder coating without warping or degrading.
-
Chemical Resistance: Evaluate the material's resistance to chemicals, including those used in the pretreatment process and any potential exposure during operation or cleaning.
-
Electrostatic Properties: Consider the material's ability to hold an electrostatic charge, which is crucial for uniform powder application and adhesion.
-
Thickness Compatibility: Confirm that the material thickness is suitable for powder coating, as excessively thin or thick materials may pose challenges.
-
Complexity of Shape: Assess whether the material's shape and complexity allow for uniform powder coverage and effective curing, especially for intricate or recessed areas.
-
Adhesion Promotion: Evaluate if any surface treatments or primers are necessary to enhance powder adhesion, particularly for materials with poor inherent adhesion properties.
-
Durability Requirements: Consider the expected use and environmental conditions to ensure the powder coating provides adequate protection and longevity for the material.
-
Regulatory Compliance: Ensure that the chosen powder coating materials and processes comply with relevant regulations and standards for safety, environmental impact, and performance.
Compliance &
Standards:
-
Adhere to environmental regulations for air quality and waste management.
-
Ensure safety standards for equipment operation and emergency protocols.
-
Handle powder materials safely for storage and disposal.
-
Regularly calibrate equipment for accurate coating application.
-
Monitor quality control for coating thickness and finish.
-
Implement waste management protocols for proper disposal.
-
Optimize energy usage for efficiency.
-
Maintain documentation for audits and reporting.
-
Provide comprehensive training for workers.
-
Continuously improve processes and equipment.