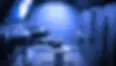
Suction Blast Cabinet
Suction blast cabinet shot blasting effectively cleans and prepares surfaces using a powerful suction system. Ideal for various materials.
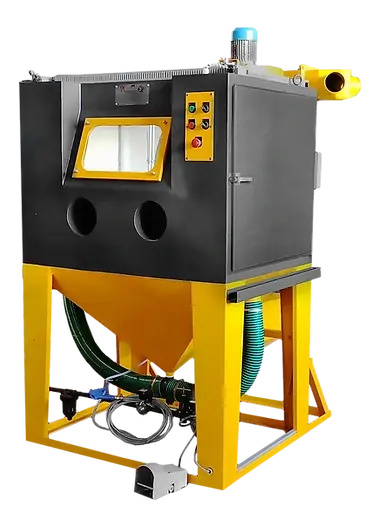
Suction Blast Cabinet
Machine
A suction blast cabinet machine is a specialized piece of equipment used in industrial settings for surface preparation, cleaning, and finishing of various materials. It typically consists of an enclosed cabinet with a viewing window, gloves for operator control, and a suction gun system.
The suction gun blasts abrasive media, such as sand, grit, or glass beads, onto the surface of the workpiece at high velocity, removing contaminants, rust, old coatings, or other unwanted materials.
The suction system then captures the used abrasive and debris, recycling it for further use or disposal. These machines are widely used in manufacturing, automotive, aerospace, and other industries where precision surface treatment is essential.
Application:
Technology:
Standard/
Customization
Delivery:
A suction blast cabinet machine uses suction to propel abrasive media onto surfaces for cleaning and preparation. It efficiently removes contaminants, rust, and paint, ensuring a clean and properly prepped surface. Ideal for various industries, it offers consistent results and ease of use in surface treatment processes.
Cabinet Type
Customised option is available as per requirement
4 to 6 weeks
Features:
-
Suction Blasting System: This is the primary feature of the machine, where abrasive media is propelled by suction through a gun or nozzle to remove material from the workpiece.
-
Cabinet Construction: The cabinet is usually made of durable materials like steel or heavy-duty plastic to withstand the abrasive environment and ensure safety for the operator.
-
Viewing Window: A transparent window allows the operator to observe the blasting process without opening the cabinet, providing visibility and control over the workpiece.
-
Glove Openings: These are built-in gloves attached to the cabinet, allowing the operator to handle the workpiece and control the blasting process without direct exposure to the abrasive media.
-
Lighting: Internal lighting provides illumination inside the cabinet, enhancing visibility and making it easier for the operator to see the workpiece and monitor the blasting process.
-
Dust Collection System: An integrated dust collection system helps to capture and contain dust and debris generated during the blasting process, maintaining a clean and safe work environment.
-
Foot Pedal Control: A foot pedal allows the operator to control the blasting process hands-free, improving efficiency and convenience during operation.
-
Adjustable Blast Pressure: Some models may feature adjustable blast pressure settings, allowing the operator to customize the intensity of the blasting process according to the requirements of the workpiece.
-
Abrasive Media Storage: Storage space within the cabinet or on the machine itself for holding abrasive media, ensuring easy access and replenishment during operation.
-
Safety Features: Various safety features such as interlocks, emergency stop buttons, and blast curtains are often incorporated to protect the operator and maintain safe working conditions.
Material Compatibility:
-
Metal: Generally compatible for cleaning and surface preparation.
-
Plastics: Exercise caution; softer plastics may deform or melt.
-
Glass: Can be processed, but avoid excessive pressure to prevent damage.
-
Wood: Not recommended due to potential surface damage and abrasive embedding.
-
Ceramics: Compatible with careful selection of abrasive media and pressure.
-
Composites: Compatibility varies based on composition; test before blasting.
-
Rubber: Not recommended as abrasive action can degrade or tear surfaces.
Compliance & Standards:
-
OSHA Standards: Follow OSHA regulations for workplace safety.
-
ANSI Standards: Adhere to ANSI guidelines for equipment design and performance.
-
NFPA Standards: Comply with NFPA standards to mitigate fire and explosion risks.
-
CE Marking: Ensure CE marking for compliance with EU directives in the EEA.
-
ISO Standards: Check for relevant ISO standards on design and safety.
-
Local Regulations: Abide by local regulations and industry-specific guidelines.
-
Industry Best Practices: Follow industry-established best practices for safe and efficient operation.