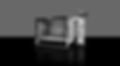
Powder Coating Booth
Introducing our advanced Batch Type Powder Coating System for high-quality finishes. Rely on us for the best solution.
Powder coating booth

Batch Type
Powder Coating System
A batch type powder coating system is a setup used in the process of applying powder coating to various surfaces. Powder coating is a dry finishing process where finely ground particles of pigment and resin are electrostatically charged and sprayed onto a surface. The charged particles adhere to the surface and are then heated to fuse and form a tough, durable coating.
In a batch type powder coating system, the coating process is carried out in batches rather than continuously. This typically involves loading the parts or components to be coated into a batch oven or booth where the powder is applied. After the coating is applied, the parts are moved to a curing oven where the powder is melted and fused onto the surface.
Batch type systems are often used for smaller-scale operations or for coating parts that require special attention or handling. They offer flexibility in terms of coating different types of parts and can be more cost-effective for smaller production volumes compared to continuous systems.
Application:
Technology:
Standard/
Customization
Delivery:
Batch type powder coating systems are commonly employed in small-scale manufacturing settings, workshops, and custom fabrication shops to efficiently coat a variety of parts and components with durable finishes, offering flexibility and cost-effectiveness for smaller production volumes.
Batch type
Powder Coating
Customised option is available as per requirement
4 to 6 weeks
Material Compatibility:
Features:
-
Versatile Booth Design: The powder coating booth is designed to accommodate a variety of part sizes and shapes. It may include adjustable racks, hangers, or fixtures to hold the parts securely during the coating process.
-
Electrostatic Powder Application: Many batch systems utilize electrostatic powder application technology, where the powder particles are charged and attracted to the grounded parts, ensuring even coverage and minimizing overspray.
-
Powder Recovery System: To minimize waste and improve efficiency, batch systems often feature a powder recovery system. This system collects excess powder from the booth or spray guns for reuse, reducing material costs.
-
Precision Control Systems: Advanced batch systems may include control systems that allow operators to adjust parameters such as powder flow rate, gun voltage, and air pressure for precise coating application.
-
Integrated Curing Oven: Batch systems typically include a curing oven where the coated parts are heated to melt and cure the powder coating. These ovens may feature programmable temperature and time controls to ensure proper curing.
-
Quick Color Change Capability: Some batch systems are designed for quick color changes, allowing operators to switch between different powder colors or formulations with minimal downtime. This feature is especially useful for facilities with frequent color changes or small batch sizes.
-
Safety Features: Batch powder coating systems are equipped with safety features to protect operators and ensure compliance with safety regulations. These may include exhaust ventilation systems to remove airborne powder particles, safety interlocks on oven doors, and emergency stop buttons.
-
Energy Efficiency: Modern batch systems may incorporate energy-efficient designs and technologies to minimize energy consumption during the coating and curing processes. This can help reduce operating costs and environmental impact.
-
Easy Maintenance: A user-friendly design with accessible components and easy-to-clean surfaces makes maintenance tasks simpler and more efficient, reducing downtime and prolonging equipment lifespan.
-
Customization Options: Depending on the specific needs of the application, batch systems may offer customization options such as additional pre-treatment stages, conveyor systems for part handling, or integration with robotic automation for increased productivity.
-
Surface Preparation: Ensure the material surface is clean, dry, and free from contaminants.
-
Heat Resistance: Materials should withstand curing temperatures typically between 300°F to 450°F (150°C to 230°C).
-
Electrostatic Charge: Metals are inherently suitable for electrostatic coating; non-conductive materials may need special treatment.
-
Dimensional Stability: Materials should maintain their shape during heating and cooling cycles.
-
Chemical Compatibility: Ensure compatibility with pre-treatment chemicals and curing conditions.
-
Adhesion: Some materials may require primers or adhesion promoters for proper coating adhesion.
Compliance &
Standards:
-
Environmental Regulations Compliance
-
Safety Standards Adherence
-
Quality Standards (e.g., ISO 9001)
-
Powder Coating Material Compliance (e.g., REACH, RoHS)
-
Equipment Safety Assurance
-
Electrostatic Discharge (ESD) Control
-
Waste Management Procedures
-
Documentation and Record-Keeping
-
Employee Training on Safety and Procedures
-
Continuous Improvement Practices