
Powder Coating - System Semi Automatic
Revolutionize your powder coating process with our amazing Semi Automatic Powder Coating System! Upgrade today for high-quality finishes every time.
Powder Coating
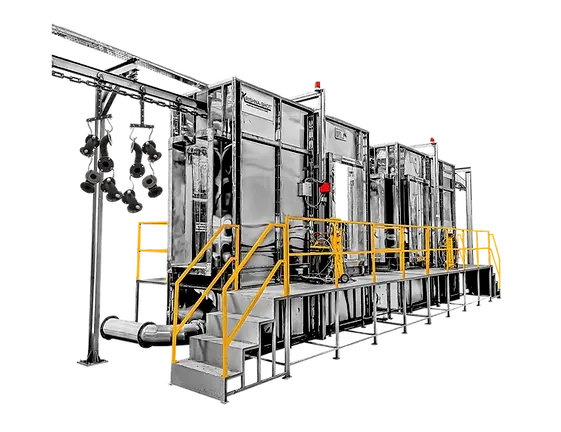.webp)
Semi Automatic Powder Coating System
A semi-automatic powder coating system represents a middle ground between manual and fully automated processes, offering efficiency while retaining some human oversight.
In this system, operators typically handle the loading and unloading of parts onto a conveyor or rack system, while automated machinery takes care of the actual powder application and curing process.
This setup allows for consistent and precise coating application while also providing flexibility for customization and adjustments as needed. Semi-automatic systems are often favored in industries where moderate to high volumes of parts need coating, striking a balance between cost-effectiveness and productivity.
By integrating automation with human intervention, these systems can deliver quality finishes while optimizing workflow efficiency.
Application:
A semi-automatic powder coating system is used in industrial applications for efficient and precise powder coating of various surfaces, offering versatility and ease of operation while ensuring uniform coverage and high-quality finishes.
Technology:
Semi Automatic Powder Coating
Standard/
Customization
Customised option is available as per requirement
Delivery:
4 to 6 weeks
Features:
-
Powder Application Gun: Semi-automatic systems typically feature a powder coating gun equipped with a powder pump and fluidizing hopper. This gun is used by operators to apply the powder coating onto the surface of the workpiece.
-
Control Panel: A user-friendly control panel allows operators to adjust settings such as powder flow rate, voltage, and airflow to optimize the coating process. It may also include presets for different types of coatings or workpiece materials.
-
Powder Recovery System: These systems often include a powder recovery booth or cyclone separator to collect over sprayed powder for reuse. This helps to minimize waste and reduce operating costs.
-
Conveyor System: Some semi-automatic systems may feature a conveyor system to transport workpieces through the coating process. This can increase efficiency by allowing continuous processing of multiple parts.
-
Curing Oven: After the powder coating is applied, workpieces need to be cured to achieve a durable finish. Semi-automatic systems may include a curing oven or infrared heating system for this purpose.
-
Safety Features: Safety is paramount in any coating operation. Semi-automatic systems may include features such as automatic shutdown in case of overheating or malfunction, as well as proper ventilation to prevent the buildup of potentially hazardous fumes.
-
Quick Color Change System: Some semi-automatic systems offer quick color change capabilities, allowing for easy switching between different powder coatings without lengthy downtime.
-
Monitoring and Quality Control: Modern semi-automatic systems may incorporate monitoring and quality control features such as digital sensors or cameras to ensure consistent coating thickness and adherence to quality standards.
-
Modularity and Expandability: Semi-automatic systems should be designed with modularity in mind, allowing for easy expansion or customization to meet changing production needs.
-
Training and Support: Comprehensive training and support materials should be provided to operators to ensure proper use and maintenance of the semi-automatic powder coating system.
Material Compatibility:
-
Metal Substrates: Typically compatible with various metals including steel, aluminum, and zinc.
-
Plastic Substrates: Some powder coatings may be suitable for certain types of plastics, but compatibility can vary widely. Conduct compatibility tests before full-scale application.
-
Wood Substrates: Generally not compatible due to the high curing temperatures required for powder coating.
-
Glass Substrates: Specialized powder coatings may be formulated for glass, but compatibility and adhesion can be challenging.
-
Ceramic Substrates: Limited compatibility due to the high curing temperatures and different material properties.
-
Pre-treatment Requirements: Substrates may need pre-treatment such as cleaning, degreasing, and applying a primer to enhance adhesion and durability.
-
Temperature Sensitivity: Powder coatings often require curing at elevated temperatures, which can impact substrate compatibility, especially for heat-sensitive materials.
-
Chemical Resistance: Consider the exposure to chemicals or environmental factors that the coated material will face and choose a powder coating accordingly.
-
Surface Preparation: Proper surface preparation, including roughening or etching, may be necessary for optimal adhesion, especially for non-metal substrates.
-
Testing and Evaluation: Always conduct compatibility tests on a small scale before full application to ensure desired results and adherence to performance requirements.
Compliance &
Standards:
-
Safety: OSHA compliance for worker safety.
-
Environment: Adherence to EPA regulations.
-
Equipment: Follow PCI or ASTM standards.
-
Electrical: NEC standards for electrical safety.
-
Materials: Use powders meeting REACH or FDA regulations.
-
Quality: ISO 9001 standards for consistent quality.
-
Training: Comprehensive operator training.
-
Documentation: Maintain records for audits.